Orthopedic implants and fixation devices run under inexorable clinical requirements – there is not even an inch of a difference in their dimensional requirements or material compatibility. From joint replacements to spinal fixation hardware, even deviations at the micron level are appreciable for the safety of patients, surgical outcomes, and reliability of long-term devices.
As orthopedic solutions become increasingly personalized and complex, achieving high-precision geometry, compatibility, and mechanical performance in the prototyping stage is non-negotiable. In the fast-paced world of medtech, rapid prototyping is essential for accelerating design iterations, refining ergonomics, and shortening time to market.
CNC machining, its unmatched precision, material versatility, and repeatability enable the production of highly functional orthopedic prototypes that meet strict medical requirements, without sacrificing speed or innovation.
Key Challenges in Orthopedic Device Prototyping
Orthopedic medical device prototyping presents several formidable engineering challenges that demand precision and specialized expertise.
Complex Geometries
Present orthopedic devices are becoming more and more individualized to the anatomies of individual patients. It’s a hip implant or a spinal cage, or a bone plate, the part needs to fit seamlessly with such complex geometries of bones. Custom-made implants tend to have complex shapes, varying thicknesses, and rich surface finishes that generic prototyping methods miss out on. In geometric dimensions in medical device prototyping, it may lead to imprecise load transmission, bad fixation, and postoperative trouble.
Material Requirements
Orthopedic devices are manufactured from difficult materials, including titanium alloy, cobalt-chrome, poly-ether-ether-ketone (PEEK), and other polymeric materials that are biocompatible. These materials are selected for their ability to be stronger and corrosion resistant, and our ability to use them in direct contact with human tissue. Prototyping them using traditional techniques like urethane casting or standard 3D printing is not challenging. Keeping mechanical performance, surface integrity, and properties of material during rapid prototyping manufacturing becomes paramount to reenact real-world use conditions.
Tight Tolerances
Dimensional tolerances in the prototyping of the orthopedic medical device are much tighter than for numerous other industries. Minimum microns of deviations may disallow joint articulation, integration of bones or hold screw in place, causing surgical failures or rejection of implants. Regulatory standards (e.g., FDA, ISO 13485) further demand traceability and reproducibility at every step. A reliable prototyping system has to guarantee clear external and internal geometries, amongst others (e.g., threads, slots, undercuts) at precise specifications, at all times.
Why CNC Machining Is the Backbone of Orthopedic Prototyping
CNC machining emerges as the primary technique in rapid prototyping manufacturing of orthopedic devices due to its remarkable accuracy, flexibility, and consistency.
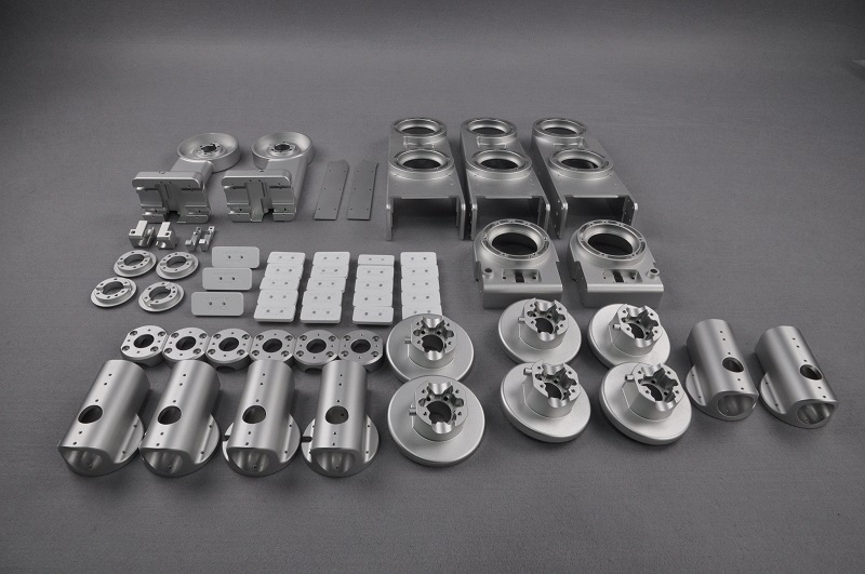
Micron-Level Precision and Repeatability
Advanced multi-Axis CNC machining systems can let them machine metals and polymers to tolerances down to ±5 – 10 microns – levels required for articulation surface of joined parts, threaded screw holes, and anatomy contours. Cuts such as undercuts, tapers, and complex cavities can be cut cleanly and predictably, passing the potential available for additive manufacturing or molding at early stages.
Ideal for Functional Prototypes and Real-World Testing
Functional prototypes that simulate the mechanical behavior of the ultimate implant are very important. CNC machining makes it possible for engineers to produce prototypes that can undergo fatigue, wear, and biocompatibility tests, mimicking a surgical environment. For example:
- Titanium spinal cages machined with CNC can be subjected to load-bearing tests.
- PEEK-based trial implants can be tested for osteointegration.
This is critical to medical device prototyping, where functional early validation assures seamless regulatory approval and fewer design iterations in the future.
Outperforms Other Methods in Structural Integrity
Although urethane casting, SLA 3D printing, and rapid injection molding play their parts in the rapid prototyping manufacturing, all are still a failure in the structural integrity of load-bearing parts.
CNC-machined prototypes are characterized by consistent density, isotropic properties of material, and an impressive surface finish, all of which are critical for orthopedic device applications where implants must resist dynamic loads and stresses.
Hybrid Approach: Combining CNC with Other Rapid Prototyping Methods
A new, lean model of medical device prototyping does not blindly use CNC machining, but intelligently adopts supplementary techniques that blend speed, cost, and functionality.
Early Concept Validation
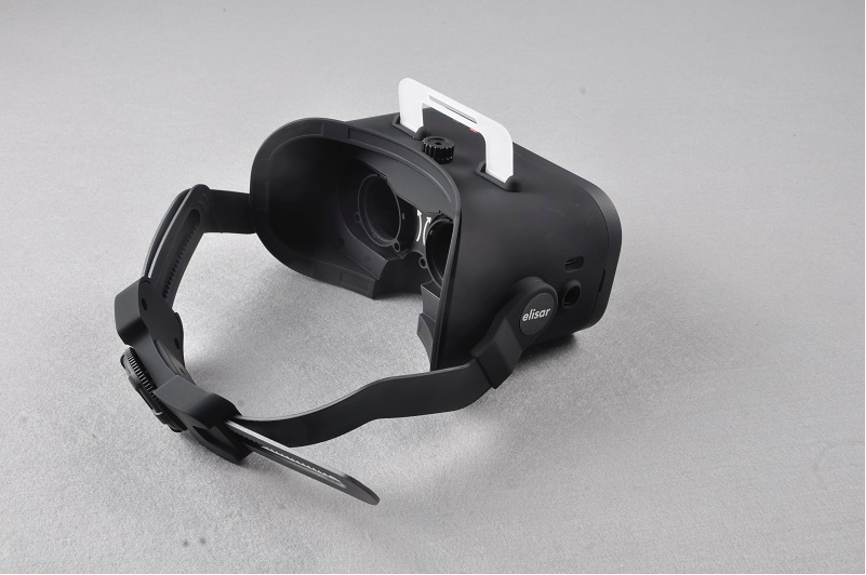
In early-stage rapid prototyping manufacturing, speed trumps strength. 3D printing (e.g., SLA, SLS) and urethane casting are valuable tools for quickly visualizing form, fit, and ergonomics of orthopedic devices. Case in point: surgeons can check the fit of a 3D printed acetabular cup or examine the ergonomics of a hand-held surgical tool before undertaking expensive CNC runs.
Conversion of functional prototypes to CNC.
After the design is validated, the design is evolved to functional testing. In this case, CNC machining steps are used to form prototypes that can be inspected while under mechanical load, sterilization cycles, and biocompatibility tests. This gradual process makes medical device prototyping efficient and clinically applicable, and each approach is optimally suitable for its purpose.
Low-Volume Trials with Rapid Injection Molding
During later stages (for instance, at clinical trials or pilot runs), the practice of combining CNC machining and rapid injection molding can find the balance between precision and scalability. For instance, external housings or non-load-bearing components (e.g., polymer-based instrument handles or alignment guides) can be high-speed, high-volume produced. Critical metal components are retained for CNC machining. This hybrid approach minimizes time-to-market and feeds regulatory submissions with representatives of production parts.
Conclusion
Orthopedic medical device prototyping requires speed, precision, and strict clinical standards. CNC machining provides the accuracy needed to prototype complex, biocompatible materials that meet regulatory demands. When paired with methods like 3D printing and rapid injection molding, it accelerates development without sacrificing quality. This integration ensures safer, more reliable devices and keeps innovation advancing in the healthcare industry.