Non-destructive testing (NDT) is a crucial aspect of quality control in manufacturing. It involves inspecting products and materials without causing damage or altering their properties. This approach ensures that products meet quality standards, are safe for use, and can withstand intended operating conditions.
NDT services are critical to ensuring product quality and safety. They can help identify defects early in the manufacturing process, thus preventing product failures, reducing costs, and mitigating risks to consumers. Additionally, NDT can be used to optimize product designs and improve manufacturing processes, leading to increased efficiency and productivity.
Thus, NDT is not only a cornerstone of quality control but also a driving force in shaping the future of manufacturing. Technological advancements have led to the development of new NDT techniques and their integration into various manufacturing processes. These developments are contributing to increased efficiency, improved product quality, and enhanced sustainability.
Advanced NDT Technologies
The field of NDT is constantly evolving, with new techniques and technologies emerging to address modern manufacturing challenges. Thermography, for example, uses infrared radiation to detect temperature variations on the surface of a material. It can be used to identify defects such as cracks, delaminations, and corrosion, which may cause changes in temperature distribution.
Another emerging NDT technique is acoustic emission testing. It involves monitoring the acoustic signals emitted by materials under stress. An analysis of these signals makes it possible to detect defects like cracks or material degradation. Acoustic emission testing is particularly useful for monitoring the behavior of materials in real-time, allowing for early detection of potential failures.
Integrating artificial intelligence (AI) and machine learning (ML) is a game-changer for NDT techniques. AI and ML algorithms can help analyze large datasets from NDT inspections, identify patterns, and predict potential failures. This can enable more accurate and efficient NDT inspections, as well as predictive maintenance.
Robotics is also playing an increasingly important role in NDT. Robotic systems can be equipped with sensors and other NDT equipment for inspections in hazardous environments or complex structures. This can improve the safety and efficiency of NDT inspections, particularly in industries like aerospace and nuclear power.
Improved Quality Control
NDT plays a crucial role in improving quality control throughout the manufacturing process. Incorporating NDT techniques into real-time monitoring systems makes it possible to detect defects as soon as they occur. Immediate corrective actions can be taken, preventing defective products from progressing in the manufacturing process and reducing the need for rework or scrap.
NDT can also be used for predictive maintenance, where potential failures are predicted and addressed before they occur. Data from NDT inspections can be analyzed to identify signs of wear and tear or other anomalies that may indicate impending failure. This allows for preventive maintenance to be scheduled, reducing the risk of unexpected equipment breakdowns and downtime.
The ability to detect defects early in manufacturing and prevent failures leads to significant cost savings. Rework and scrap can be expensive and time-consuming, and by reducing the occurrence of these issues, NDT can improve overall manufacturing efficiency and profitability.
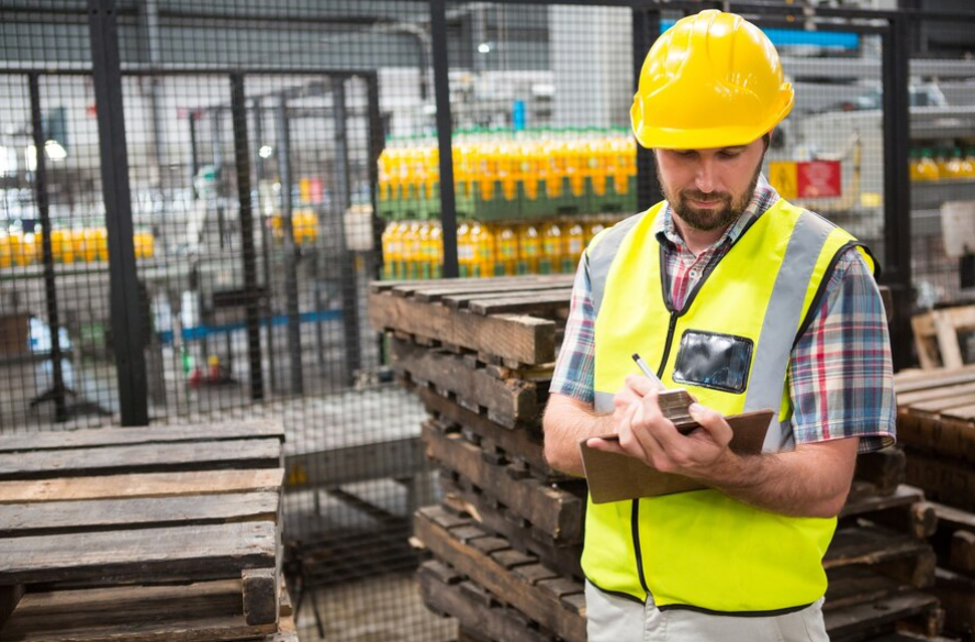
Enhanced Product Safety
NDT is also essential for ensuring product safety. The technique helps identify potential hazards and risks to prevent accidents and injuries. For instance, NDT can be used to detect defects in critical components like pressure vessels or structural elements, which could lead to catastrophic failures if left unchecked.
NDT is also crucial to ensuring compliance with industry standards and regulations. Many industries have specific product quality and safety requirements, and NDT is often used to verify compliance with these standards. NDT demonstrates that products meet the required standards, thus helping protect consumers and ensure the safety of products on the market.
Apart from protecting consumers, NDT also contributes to environmental protection. It identifies and addresses defects that could lead to environmental hazards, thus preventing pollution and protecting natural resources. For instance, NDT can detect corrosion in pipelines or storage tanks, preventing leaks that could contaminate the environment.
Increased Efficiency and Productivity
Integrating NDT into manufacturing processes can significantly improve efficiency and productivity. Automating NDT inspections helps organizations reduce the time and labor required for quality control. Automated systems can perform inspections more quickly and consistently than manual methods, leading to faster turnaround times and reduced bottlenecks in the manufacturing process.
NDT data can also be used to improve decision-making. Organizations can analyze NDT data to gain valuable insights into the performance of their products and processes. This data can be used to identify areas for improvement, optimize manufacturing processes, and reduce waste.
To improve efficiency and productivity, it helps organizations remain competitive in today’s global market. Faster turnaround times, reduced costs, and improved product quality are all benefits that can be achieved through the effective use of NDT.
Sustainable Manufacturing
NDT is also crucial role in promoting sustainable manufacturing practices. Nondestructive testing techniques help identify defects and optimize manufacturing processes, thus reducing waste and conserving resources. Defects in materials that could be recycled or reused can be effectively detected, reducing the need for new materials.
NDT can also monitor energy consumption and identify areas where energy efficiency can be improved. It helps optimize manufacturing processes and reduce energy consumption, thus reducing the environmental impact of manufacturing operations.
NDT also contributes to a circular economy by enabling the reuse and recycling of materials. Defects can be identified and material conditions assessed, thus helping determine whether they can be reused or recycled. This can reduce the demand for new materials and minimize waste, promoting a more sustainable manufacturing model.
Conclusion
Non-destructive testing (NDT) offers numerous benefits to the manufacturing industry. It helps ensure product quality, safety, and efficiency, thus paving the way for both more competitiveness and sustainability. NDT can help reduce costs, improve product performance, and minimize environmental impact.
The future of NDT is bright, with ongoing advancements in technology and techniques. New NDT methods are on the horizon, and existing techniques are being refined to address the evolving needs of the manufacturing industry. Integrating NDT with other technologies like artificial intelligence and robotics will further enhance its capabilities and benefits.
As manufacturing continues to evolve, NDT will remain an essential tool for ensuring product quality and safety. Organizations that embrace NDT and invest in advanced technologies can position themselves for success in a competitive and sustainable manufacturing landscape.